Please click here to access the main AHDB website and other sectors.
The benefits of lean techniques in horticulture
Tuesday, 17 November 2020
Find out how a few quick, cheap and easy fixes helped save one broccoli producer both time and money in their packhouse by implementing lean techniques.
For many horticultural businesses, the challenge of accessing reliable and affordable labour is one of their biggest concerns.
In response, AHDB developed SmartHort, a programme to help growers make improvements to their labour efficiencies and to investigate new automation and technologies.
As part of this activity, three Strategic SmartHort Centres were launched to demonstrate practical ways of introducing lean techniques to horticultural businesses of any size or crop.
Willie Russell, from Easter Grangemuir Farm, Fife was one of the growers who took part. Here, he explains how his business benefited from the workshops.
About Easter Grangemuir Farm
- Crops: Fruit, vegetable, potato and arable
- Location: East Neuk, Fife
- Labour: Relies heavily on overseas labour
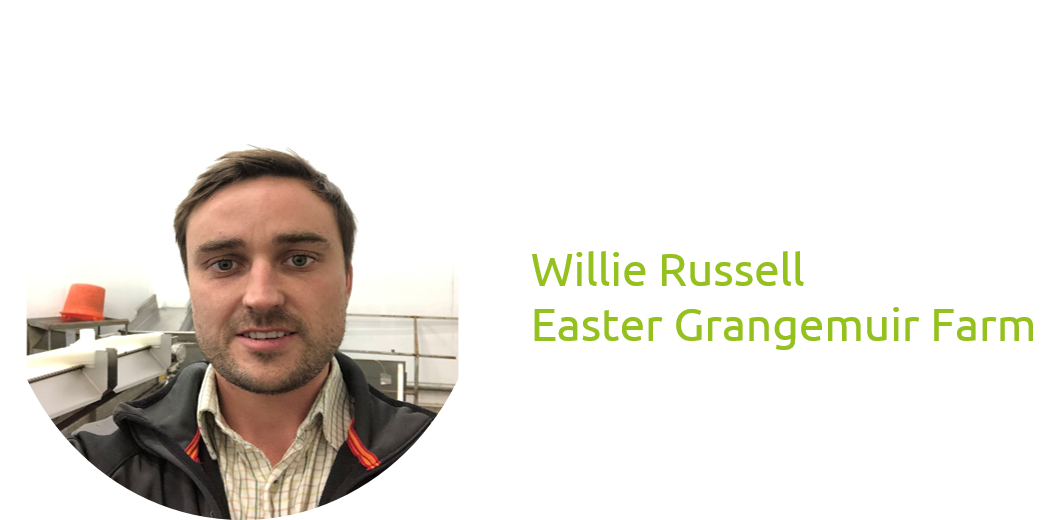
What are Strategic SmartHort Centres?
Developing staff skills is a key priority for the farm. Willie became involved with Thomas Thompson Strategic SmartHort Centre in Perthshire at the suggestion of colleagues.
“Much of my time is spent managing people and processes, looking for ways to reduce our costs while continuing to produce quality products,” said Willie.
The workshops introduced the key principles of lean, including;
- Pull systems to make the supply chain more efficient
- Visual management aids to trigger when to order new stock
- Reorganised workspace to reduce the walking and waiting time
Willie found the ‘waste walks’, which look at where efficiencies can be made in the business, particularly useful.
“The information has always been in front of us in plain view, but it took this course to help me process it and work out how to alter certain areas of the business to become more efficient.
“It has made it easy to see on paper where the business could be more effective and what is effective already,” Willie stated.
Participants were encouraged to put the lean principles shown at the centres into practice in their own businesses. In Willie’s case, he focused on broccoli production, specifically looking at the packhouse.
“Broccoli production is labour intensive and any way we can cut down the costs and become more efficient is positive,” he explained.
Positive changes
Some of the changes Willie has implemented have already had a substantial impact.
“The changes I’ve made include placing a whiteboard in the packhouse with the day’s orders on it so that it is visible for everyone. This has reduced the downtime changing from one order to another. When the forklift driver is not busy, he looks at the order and prepares the boxes or crates that will be used for the next order. This has saved 5–10 minutes per order switch.
“Making the flow of broccoli to the broccoli stalk trimmers continuous has made the process more efficient too. This was an easy fix, by training the stalk trimmers how to do their job smoothly.
“Implementing Kanban, a new way of scheduling, has been a huge positive in the overall production system, meaning less downtime.
“The next step is to look over the whole business and see if there are other quick fixes that can be done to lower costs and become more efficient. I am also going to have a meeting with my colleagues and hopefully train them in lean principles.”
How do I get involved?
Willie is keen to encourage others in the horticulture sector to get involved with SmartHort.
“I would 100% recommend this project to every business, no matter what size you are. This programme of work trains you to think about your business differently. It makes you realise the little things that, in the past, you have noticed but not identified as a bottleneck or an inefficiency.
“With costs going up for everything, apart from our product, we, as farmers, need to work on how to cut costs, while still producing a quality product.”
“The workshops have been a great experience for me. I’ve enjoyed meeting new people and broadening my mind on how other businesses work and how other products are produced,” he said.
“My favourite part, so far, has been the fantastic conversations that we have all had about how we do a certain task in our operation compared with how other businesses do it.
“No matter what the product, I have been able to extract small points from the conversation and use them to my advantage.”