Please click here to access the main AHDB website and other sectors.
Lean, labour and Lego: Boosting labour productivity in horticulture
Tuesday, 30 July 2019
How can playing with Lego boost labour productivity in horticulture? Delegates at the first Strategic SmartHort Centre held this summer, found out.
When was the last time you played with Lego? Growers attending the first Strategic SmartHort Centre workshop were willing to embrace their inner child to play a game with Lego bricks to simulate a horticulture business, with impressive results.
The exercise introduced the group to some of the key principles of LEAN; pull systems to make the supply chain more efficient, visual management aids to trigger when to order new stock and testing a reorganised workspace to potentially reduce the amount of time wasted walking and waiting. The simulated production lead time improved by almost 70% and the productivity per person increased by 333%.
And while this was just a game, it helped to re-enforce the message that small changes in a production system to reduce waste can have a significant impact.
What is LEAN?
Neil Fedden, Fedden USP, who is leading the Strategic SmartHort Centres, said: “LEAN isn’t just about seismic shifts or completely overhauling your operation, it’s also about lots of small incremental improvements across the whole operation. It’s about understanding where the true value is, that is what your customer is willing to pay for. Everything else in your process could be considered waste and LEAN helps you to reduce that through small changes.”
Lessons from Volmary
Volmary, Wisbech, is acting as a ‘live case study’ as part of their role as SmartHort Strategic Centre hosts. It is an independent, growing family business that propagates many millions of bedding plants, perennials, shrubs, vegetables and herbs. At peak production at the Wisbech site, sticking alone is over 2m cuttings a week. Almost 70% of their business takes place in just 3 months of the year. Dealing with these seasonal peaks, with a challenging labour market (30% of seasonal staff offered employment last year, didn’t turn up to work), was one of the reasons they signed up to the SmartHort programme.
Throughout the year, we will be working with Volmary to introduce LEAN techniques to two production areas: potting and sticking. The processes were analysed using techniques from the LEAN toolbox by growers attending the workshop. They counted, timed and paced out the operations to create a process map and used a 10-second interval observation technique, called Activity Sampling, to capture what actually happens real-time in the process over a 20-minute period.
One of the eye-opening moments was following the ‘journey’ of a cutting. The only element of the process that adds value, the part the customer is willing to pay for, is sticking the cutting in the compost-filled tray, which takes just one second to complete. Within their current process, the lead time for the cutting from refrigeration to plug is 7,016 seconds.
Neil said: “The percentage of value added within a process is always extremely low, but it’s an incredibly useful tool to make people think about their production in a new way. We can now ask where in those other 7,015 seconds is there potential to reduce the wasted time.
“The tools give you an objective data set that you can analyse. It’s only when you stand back and watch yourself identify the problems – you often can’t see issues when you work with them every day.”
The next step for Volmary is to put together an action plan, based on some of the areas the group identified. Suggested changes ranged from introducing height-adjustable individual working stations, having different colour trays for different cutting types and bringing in a portable fridge to reduce the walking time from the glasshouse bay to where the cuttings are stored.
Another key area identified was how to free up key personnel to invest more time in training and optimising new agency staff. There can be a 25% variance in the number of trays of cuttings achieved by the best and worst workers, so helping to close that gap could make a big difference.
Shirley Barber, who supervises sticking production at Volmary, said: “As a business, we are continuing to grow. We have previously identified some improvements that could be made, even before this workshop, but the tools we have been given today help us to evidence the cost benefit of investing to make those changes.”
The cost/benefit analysis of the potential improvements identified in a process is a critical part of LEAN. While introducing an automated conveyor belt could help to reduce the amount of time staff are walking back and forth, will the investment off-set that labour cost? Using a prioritisation matrix, another LEAN tool, businesses can identify where the quick wins and biggest impact can come from.
If you’re interested in finding out how to implement LEAN into your business, contact grace.emeny@ahdb.org.uk or visit ahdb.org.uk/smarthort where resources from the workshops will be available.
To find your nearest Strategic SmartHort Centre and to book your place, visit our event listings page.
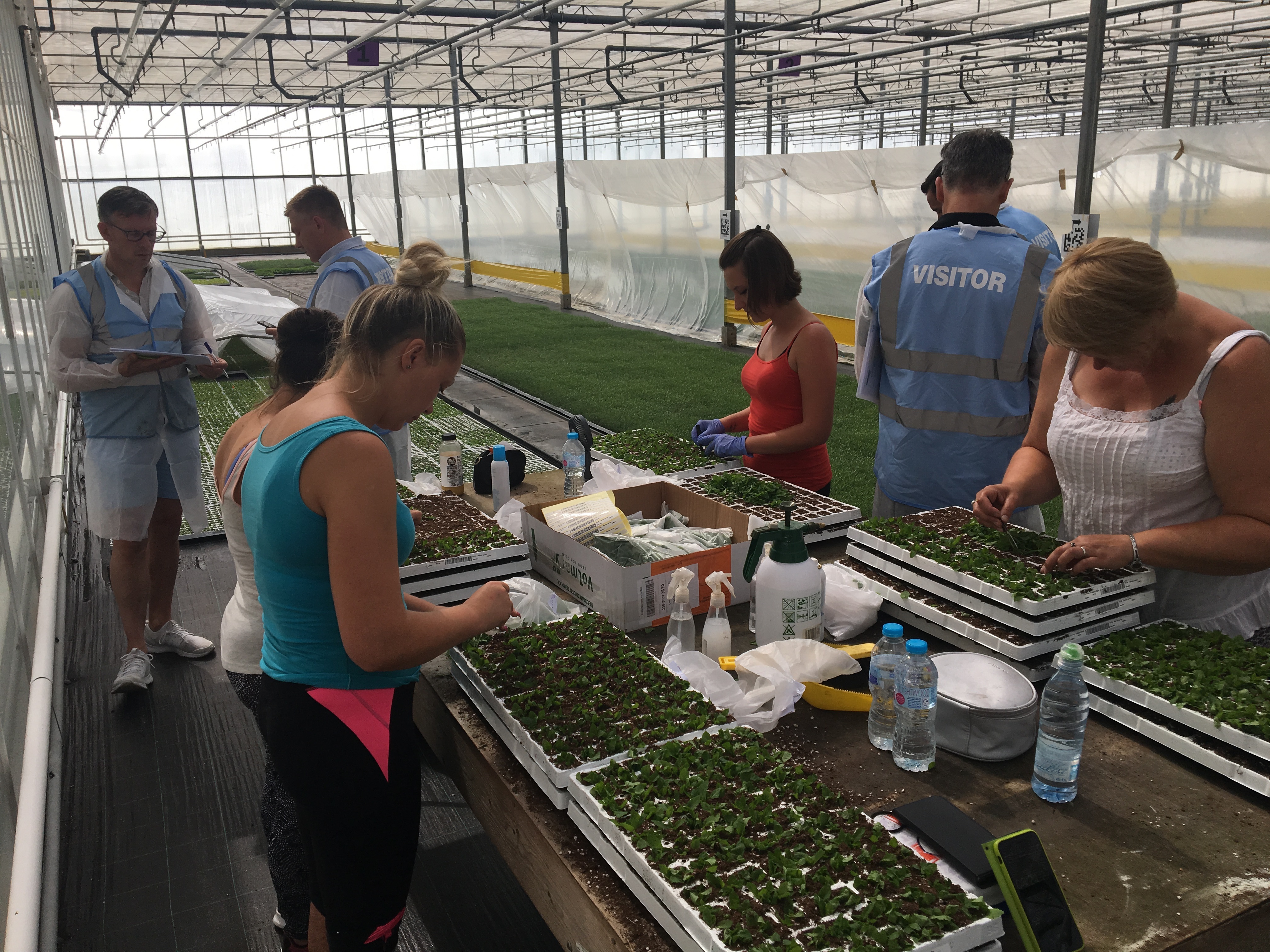
Typical LEAN projects for horticulture
- Reducing set-up times with production that involves lots of different varieties
- Reducing the lead time to despatch
- Coping with seasonal spikes
- Improving communication with back office and production staff in complex changing businesses
- Organising workplaces with expanding volumes, with spaces that aren’t able to also grow