Please click here to access the main AHDB website and other sectors.
- Home
- Knowledge library
- Using the Kanban framework to improve business efficiency
Using the Kanban framework to improve business efficiency
Find out how you can use the Kanban framework to manage critical tasks and improve your business efficiency.
What is Kanban?
Kanban is a Lean management framework used to manage work and improve efficiency. It is a Japanese term that translates into ‘visual sign’.
Kanban boards can be used to visualise and manage critical tasks, helping you identify areas that need improvement.
The boards can help you see quickly all the tasks necessary to reach your end goal. They can make it easier to spot tasks and processes that could cause delays, which you can then consider prioritising as areas for improvement.
Targeting the most detrimental parts of any process will result in the most significant improvements in business efficiency; this is referred to as the Pareto Principle.
Using Kanban boards
Kanban boards may be used with anything that involves a process.
You use the boards to divide tasks into three categories:
To do | Doing | Done |
Tasks always begin on the left-hand side of the board and finish on the right.
For example, the process of preparing for a factory deep clean involves many tasks.
The Kanban board represents the process, and so before you start, you would add all of the individual tasks associated with the deep clean in the ‘to do’ column.
Some tasks may take longer than others, but they should all be captured.
To do | Doing | Done |
Unplug all electricals Buy cleaning materials Dismantle equipment |
Once all the tasks associated with the process have been added to the board, work can begin. As each task is started, it moves into the ‘doing’ column.
Depending on the complexity of each task, some may move across the board quickly, while others may remain in the ‘doing’ column for some time. It is helpful to record the amount of time that each task takes, as this will help you identify the most time-consuming parts of the process, and any bottlenecks.
To do | Doing | Done |
Dismantle equipment |
Unplug all electricals Buy cleaning materials |
Using this example, the purchasing of cleaning materials and unplugging electricals might not take very long. However, dismantling equipment could be very time-consuming.
To do | Doing | Done |
Dismantle equipment |
Unplug all electricals Buy cleaning materials |
When you can visualise the whole process, you can spot which tasks are more time-consuming than others and which are holding things up.
In the example, dismantling equipment is the most time-consuming task and creates a bottleneck.
One way of improving the efficiency of this task and the overall process could be to train more team members to dismantle the equipment.
Another option could be to start this task earlier in future as it takes longer than the other processes identified.
To do | Doing | Done |
Unplug all electricals Buy cleaning materials Dismantle equipment |
Once all tasks are complete, they should be placed in the ‘done’ column on the Kanban board.
Kanban in practice
For complex processes, there may be hundreds of tasks associated with it, for example, the construction of a building.
A whiteboard and sticky notes are commonly used for the Kanban method. However, digital Kanban platforms are available and can be more practical for large-scale processes.
When a lot of tasks need completing, it is useful to prioritise your ‘to do’ column into the following categories:
- Urgent, critical: Must be done soon and not doing it will have serious consequences.
- Urgent, non-critical: Must be done soon and not doing it will be an inconvenience.
- Non-urgent, critical: Doesn't have to be done soon, but if the deadline is missed, it will have serious consequences.
- Non-urgent, non-critical: Nice to do, but has little impact or consequence (vanity projects).
This would produce a Kanban board that looks like the one below.
To do | Doing | Done | |
UC | UNC | ||
NUC | NUNC |
Those tasks in ‘urgent, critical’ (UC) should be the first to move into the ‘doing’ stage. Non-urgent, non-critical (NUNC) should be the last to move and only when there is a period of low labour requirement.
Adapting the Kanban board
It is common for Kanban boards to be adapted to suit different situations. Common changes include:
- Colour coding to represent which individual, team or department is working on specific tasks
- Highlighting certain tasks to represent low or high priority
- Adding dates/times to tasks to say when they need to be completed
- Work-in-progress limits can restrict how many tasks are in different workflow stages and get things finished more quickly by focusing on fewer tasks at once
Identifying bottlenecks
Kanban boards help identify problems in any process. If a task is stuck in a column for a long time or a lot of tasks assigned to a specific person or department mount up, it becomes clear where the bottleneck is.
Once you have identified this, you can put measures in place to resolve it and prevent it from reoccurring. A helpful method you can use to resolve bottlenecks is the Root Cause Analysis technique.
Find out how you can use Root Cause Analysis to resolve issues
Useful links
Lean management for farmers and growers
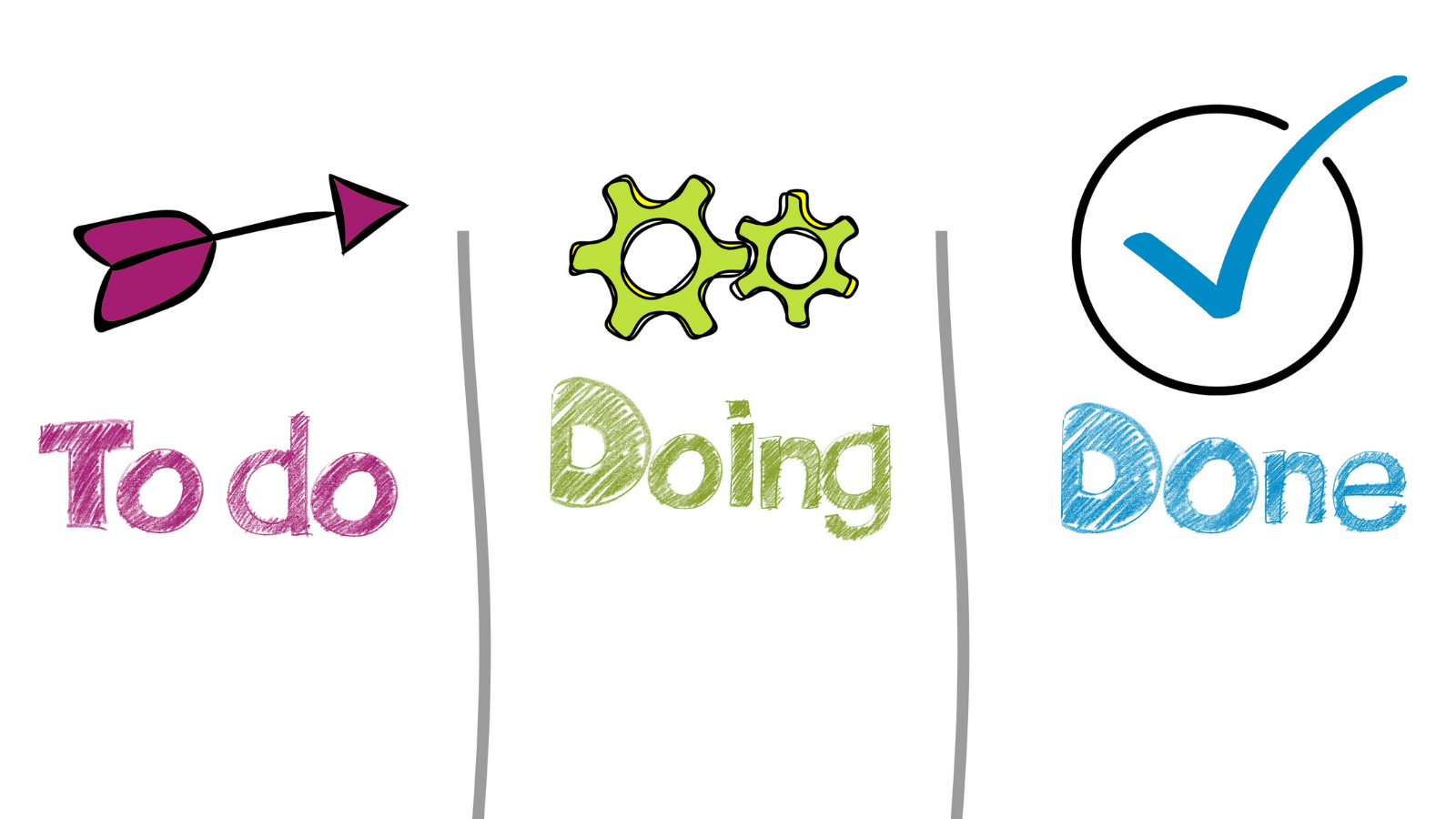
Topics:
Sectors:
Tags: