Please click here to access the main AHDB website and other sectors.
- Home
- Knowledge library
- Seven C's for irrigation efficiency: core equipment
Seven C's for irrigation efficiency: core equipment
It is worth considering the primary energy drivers for irrigation systems and how your core equipment affects this. Read on to find out more.
Back to: Irrigation energy efficiency
A system’s energy use is directly proportional to the volume of water it moves and the pressure against which the pumps must operate. Double the volume or the pressure, and the energy use in delivering the water also doubles. So, if either of these factors can be reduced, less energy will be used.
What actions can you take?
Here are some ideas about how to reduce your core equipment energy use.
Volume of water
The volume of water use is critical, and this will be looked at in a little more depth when we consider ‘Containment’ and ‘Control’ in the Seven ‘C’s approach.
Reducing pressure
Reducing pressure is linked to three primary factors:
Connecting pipe size and the pressure drop through the delivery system
If the water velocity through the pipes and joints is too high, then water pressure losses are high. Likewise, if filters are too small or become blocked, more energy is needed to overcome them. The important thing here is to measure the pressure in the system at different points to determine where pressure is being lost. Any more than 20% might be seen as excessive.
Final Delivery System
There are big differences between systems that use spray nozzles and those which provide drip irrigation. Generally, spray systems have a pressure requirement between four and ten times greater than drip delivery systems. This relates directly to energy use, so the choice of the system at the design stage has obvious long-term energy implications.
Primary Feed System
Here we are concerned about the choice of pump and how it can work flexibly with the final delivery system:
- Pumps must have a characteristic such that maximum efficiency is reached at around the pressure and volume required by the system. If pumps are badly specified, they may be operating considerably below their efficiency sweet spot. So, for instance, using a high-pressure pump on a low-pressure system may still deliver the volume of water required, but energy use per unit of water delivered will be higher than it should be. Check your system operating pressure against the manufacturer’s efficiency curve for your pump to see what efficiency you are achieving
- Pumps should be fitted with the most efficient motors. Electric motors have always been efficient, but new pumps are marginally better than older designs (probably 2 or 3% better). Over the life of the pump, the cost savings from the high-efficiency motor type may be worth an upgrade
11 kW pump running 30% of the time will cost £4,500 per annum. A 3% saving would be £135 per year, giving £2,025 savings over the expected lifetime of 15 years.
- Pump systems must be able to respond to changing volume and pressure requirement caused by different levels of irrigation and changing irrigation location. For a ‘fixed speed’ pump, this is a big ask, and in the past, the only way to deliver this has been through the use of pressure relief valves to bleed-off some of the extra pressure or volume delivered by a pump with restricted output requirement. Although this is effective, it is not energy efficient. It’s now commonplace to deal with this problem by using variable speed pumps (with inverter drives), which are modulated to deliver a fixed system pressure. This can have a really big effect on energy use. On large irrigation systems, research has shown a reduction of up to 50% in annualised running costs can be achieved
Useful links
Visit our GrowSave pages to read more about how you can save energy and improve efficiencies
Go to: Seven C's for irrigation efficiency: control, containment and counting
Go to: Seven C's for irrigation efficiency: care, cost, create
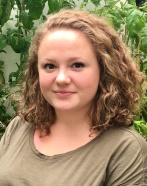
Topics:
Sectors:
Tags: