Please click here to access the main AHDB website and other sectors.
- Home
- Knowledge library
- CO2 Best practice guide: Sources of CO2
CO2 Best practice guide: Sources of CO2
Natural-gas boilers
Flue gases from natural-gas boilers are widely used in UK horticulture as a source of CO2 for enrichment. They are initially very hot and have to be cooled before being introduced into the glasshouse. This is done by mixing the exhaust with fresh air or by passing it through a flue gas condenser. This source of CO2 is generally thought to be sufficiently ‘clean’ to require no further treatment. The production of 1 kg of CO2 requires the burning of 5.41 kWh of natural gas and, assuming a cost of £1.75p/kWh for natural gas, each kg of CO2 that is generated purely to enable enrichment will cost around 9.5p. At an 85% boiler efficiency level, 4.6 kWh of hot water is also produced.
CHP installations
The exhaust gases from CHP units can also be used to supply CO2 for enrichment, together with heat and electricity. They are highly efficient, typically converting over 90% of the input fuel into heat and electricity, and produce more CO2 per unit of heat output than a glasshouse boiler. However, most of the units installed on UK nurseries use natural-gas-fuelled reciprocating engine generators with outputs in the range of 1–4 MW (electrical output), and it is necessary to incorporate catalytic converters to ‘clean up’ the exhaust gases before these can be used in the glasshouse. This inevitably adds to the cost of the installation.
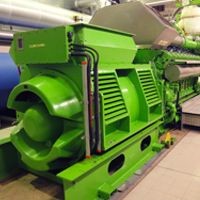
Biomass boilers
Although it is theoretically feasible to recover CO2 from the flue gases of combusted biomass fuels (e.g. woodchip, straw, etc.), the technology to do this is in its infancy. One of the few nurseries using biomass flue gases for CO2 is in Vancouver, Canada, and it uses ProSelect GC6. Find more details about biomass boilers on the GrowSave website. Currently, if biomass fuels are being considered, alternative sources of CO2 will need to be sought. A feasible option could be to use two boilers and a combination of fuels, such as wood alongside natural gas. The low-carbon (and, hopefully, lower-cost) biomass fuel would deliver the baseload heating at times when CO2 demands were low, but the grower would switch to (or use as a top-up) the cleaner-burning natural gas (and flue gases) at times of high CO2 demand. An alternative would be to use pure CO2 alongside a renewable-fuel-fired boiler, but this may be cost-prohibitive.
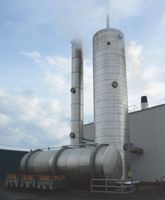
CO2 burners
CO2 burners (air heaters) differ from heating boilers in that they are suspended within the glasshouse above growing crops. They typically burn LPG (propane) or kerosene but can be operated on natural gas. As well as generating CO2, burners produce water vapour and this can raise glasshouse humidity. They also produce heat and this will offset glasshouse heating costs in winter. Regular maintenance is essential to prevent incomplete combustion and incorrect flame temperature since these result in the production of aerial pollutants. It may be necessary in well-sealed houses to provide the burners with their own outside air supply. A particular problem with CO2 burners is that it is frequently difficult to adjust the CO2 output, making control very difficult and leading to CO2 gradients within the house.
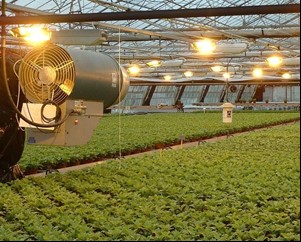
Pure CO2
Pure CO2 can be obtained in liquefied form as a by-product of industrial processes. This source of CO2 has the advantage of being free of injurious pollutants. It can also be used independently of the need for glasshouse heating and is easily piped into the glasshouse. A certified bulk storage tank is required.
New CO2 sources
Growers have also started to use anaerobic digestion as a means of generating gas to heat glasshouses which also directly produce CO2. Quality of feedstock and suitable purification systems both need attention to ensure a suitable supply of CO2 to the glasshouse from AD plants. More information on the current status of CO2 can be found on the GrowSave website.
Sectors: